The Difference Between Polyester and Vinylester Chemical Anchoring


Why is Chemical Anchoring confusing?
All information in this article is very broad, general information. Please contact an engineer for any safety critical applications or contact the manufacturer direct for brand specific information and application data.
The main reason why chemical anchoring is so confusing, is that all the manufacturers and distributors all over the world call their chemical wildly different names that usually have little to no bearing on what the product actually is or how it performs.
Most (including us) call them some variation of a part code and there isn't usually much more information to go off without contacting your local rep or doing some extensive google searching. Example Brands: Powers AC100E or the Ramset Chemset101 etc etc
With manufacturers and distributors all having totally different naming conventions for their chemical ranges it's exceptionally difficult sometimes to fully understand what you're buying, which one you should be buying and what the differing benefits are between brands or even between various types of the same brand.
There is, a method to the madness though and a reason why this happens.
Suppliers tend to call their chemical some variation of a part code for specifying reasons. Once an engineer or architect has drawn onto the plans (specified) 'use this type of chemical: Random Chemical Brand 108759' then this cannot be broken and must be used by the builder or contractor.
'Big' jobs where engineers and architects are nearly always involved account for most of the sales volume when it comes to chemical anchoring. This means that there is very little incentive for the manufacturer to make their product easily understable to the end user, as in most cases, manufacturers or distributors will deal directly with the engineers to have their product be the 'go to' when drawing plans and therefore by default, must be used on the job.
It is a key point to state that some manufacturers may actually keep their chemical anchoring ranges confusing for a reason.
Once an engineer or architect is happy with the product and performance, increasing the overall difficulty in understanding the various brands, ranges and benefits may be off putting to some and may just be off putting enough to keep that particular engineer continually specifying the same chemical for years on end without ever looking anywhere else.
What is Chemical Anchoring?
Chemical anchoring is what we call injection mortar, or concrete glue, for lack of a better term. Chemical anchoring is used to 'glue' into masonry, studs, bolts and threaded rod usually.
Chemical anchors are pretty much the strongest type of concrete fixing available on the market. It's generally used on large scale construction projects for safety critical applications where the anchor will be under large forces.
We tend to move customers onto chemical anchoring as a catch all, where ever you have an application with forces over a couple hundred kgs, you generally can't go wrong with chemical anchoring.
The Main Types of Chemical:
There are 100's of different types of chemical anchoring available on the market, all with slightly different chemical compositions and differing load data.
The big 4 are:
- Polyester
- Epoxy acrylate also known as Vinyl ester
- Pure epoxy
- Hybrid systems
The two main and most broadly used types though are polyester based chemical anchoring and vinyl ester (or epoxy) type chemical anchoring.
For the sake of keeping this article brief, we'll focus on these two types. You can find a significantly more in-depth article here on the chemical composition differences between these two: Vinyl Ester vs Polyester Resins there is also an australia drawn document that is more in depth here: The chemistry of chemical anchors: how different chemical formulae affect the installability and long-term performance of chemical anchors
Polyester Chemical
Polyester type chemical was the first type of chemical anchor developed and involves a 2 component injection system in which a polyester resin mix is mixed with a reactive solvent (also called monomer in the chemisty world or a 'catalyst'). For any of you who have used car bondo, or bog before, think glue plus hardener.
When pushing the chemical anchoring through the nozzle, the inbuilt mixers mix the polyester base with the reactive solvent to form the injection mortar.
Vinyl Ester Chemical
Again the same format is used for delivery (2 part injection system), except rather than a polyester based mix these chemical are a epoxy acrylate (referred to as vinyl ester) mix. This is installed exactly the same as polyester type chemicals.
Whats the differences between the two?
There is a few key differences between the two types although they are both probably equally as popular
- Vinyl ester will out perform polyester in terms of load ratings. Although both still have exceptionally high load ratings.
- Vinyl ester can be used in application where water is present (although not under water, it is water repellent)
- Both types of chemical can have some shrinkage effect, although this is significantly less prevalent in vinyl ester.
- Polyester is generally cheaper than Vinyl Ester and we find is more freely available in the marketplace.
- Polyester will cure or 'set' quicker than Vinyl Ester.
- Vinyl Ester type chemical can be used in lower temperature ranges than Polyester.
Heres a chart we've drawn up to display the biggest moving brands and types here in Australia and which type of chemical anchoring they are:
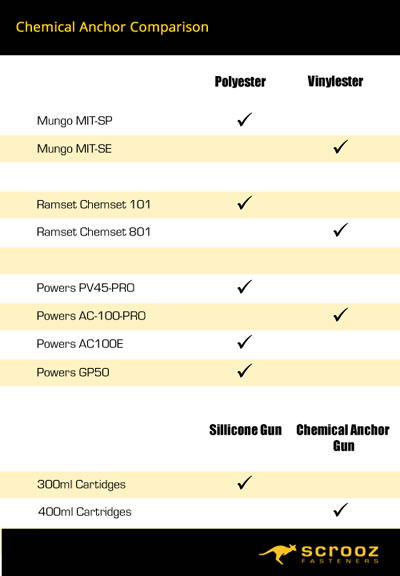